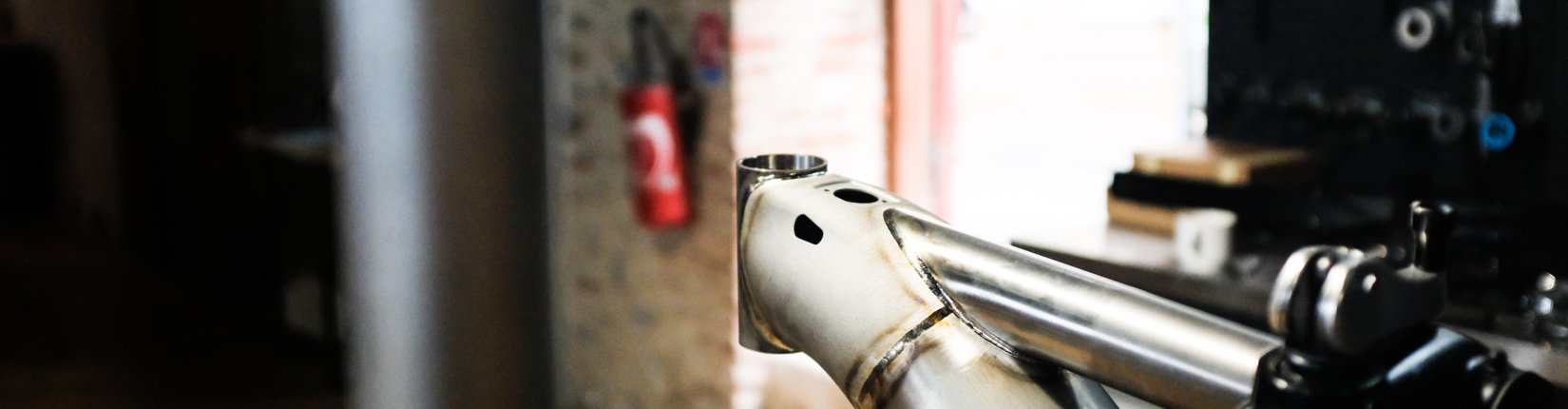
Impression 3D mitigée
Ces derniers temps, nous voyons de plus en plus de vélos d’artisans utiliser l’impression 3D, ou plutôt faudrait-il dire la fabrication additive, pour réaliser certaines pièces complexes d’un cadre.
Chez Caminade nous avions présenté le One4all au Roc D’Azur dès 2016 dans sa version Expresso ( soudé au TIG ) qui disposait de 5 pièces imprimées 3D en acier Maraging. A l’époque, il y avait 2 raisons à cette évolution :
- rigidifier les zones de pivot
- simplifier le process de fabrication
A l'époque nous avions utilisé la seule technologie disponible, la DMLS qui consiste à fusionner partiellement de la poudre métallique grain par grain et couche par couche avant de fusionner définitivement l'ensemble dans un four. Mais le coût du cadre en était pénalisé à cause du coût de revient, plus lié au temps de fabrication ( pourtant automatique ) qu'au prix de la matière.
https://youtu.be/lIYyUxtYxFQ?si=BShXWmYB6tp5VguT
Cette techno nous a permis de sortir une version titane du one4all avec un poids réduit de 40% mais un coût augmenté d’autant, ainsi qu'un concept bike de cadre manchonné/collé en Scalmalloy qui a servi de base à la techno injecté/collé de notre AllRoad, mais sans l'aide de la fabrication additive puisque les manchons en Composite de carbone fibre longue (10mm ) et de Polyamide sont obtenus par injection.
Pourquoi voit-on augmenter l’utilisation de la fabrication additive dans le vélo artisanal ?
Deux raisons à cela. La première est l’évolution des techniques, la poudre a d’abord fait place à des granulés ( FGF ) et depuis peu a du fils chargé ( FDM ) évitant les risques d’intoxication liés à l'inhalation de la poudre de titane, et permettant l’utilisation de machines moins complexes ( car sans laser de frittage ) donc moins couteuses.
- La poudre métallique est donc mélangée ( fixée ) dans un liant qui facilitera son agrégation pour former une pièce en volume légèrement plus grande pour tenir compte du retrait, comme en moulage mais pouvant aller jusqu’à 15%.
- La pièce ainsi obtenue est "déliantée" dans un bain dont le liquide va dépendre de la matière à dissoudre, mais le plus souvent de l'acétone dans un bac à ultra-sons.
- La pièce, encore fragile, va ensuite être frittée ( soudure des grains ) pour obtenir une pièce poreuse à 5% mais solide. Dans le cas du titane, le four devra être sous atmosphère neutre comme lors de la soudure TIG.
- Reste le travail de finition, d’état de surface, mais surtout de tolérance car la répétabilité n’est pas encore le point fort de la fabrication additive métallique, surtout dans sa version FDM.
Les meilleures machines industrielles utilisent actuellement la technologie SLM qui fusionne définitivement la poudre à l'aide d'un laser plus puissant. Plus coûteuse, mais au ratio tolérance/résistance/prix le plus équilibré. Pourtant un jeu de 6 manchons en titane fabriqué en France ( comme ceux de notre LongRoad, mais plus fins ) coûterait 4500€ chez Protolabs qui fabrique déjà nos manchons injectés pour 10 fois moins !
What the fuck ?
La réponse est arrivée par mail d’Asie sous la forme d'un démarchage commercial pour un cadre titane déjà soudé à l'aide de nombreuses pièces imprimées en 3D lui donnant un aspect de cadre carbone monocoque : un bel objet pas cher du tout, qui nous a permis de comprendre que les Asiatiques, malgré leur faible coup de main d’œuvre, possédaient aussi des imprimantes 3D métalliques. Fourche, pédalier, douille, tige de selle… ils peuvent tout faire et pour un prix 5 fois moindre qu’en France.
Alors je vous le demande, doit-on céder aux sirènes asiatiques de l’impression 3D ? ou comme pour les autres composants du vélo, doit-on continuer à sourcer au plus près, quitte à investir 120k€ dans une machine fabriquée en France, mais au risque de nous éloigner de l'artisanat ?
Parution : 19/11/2023