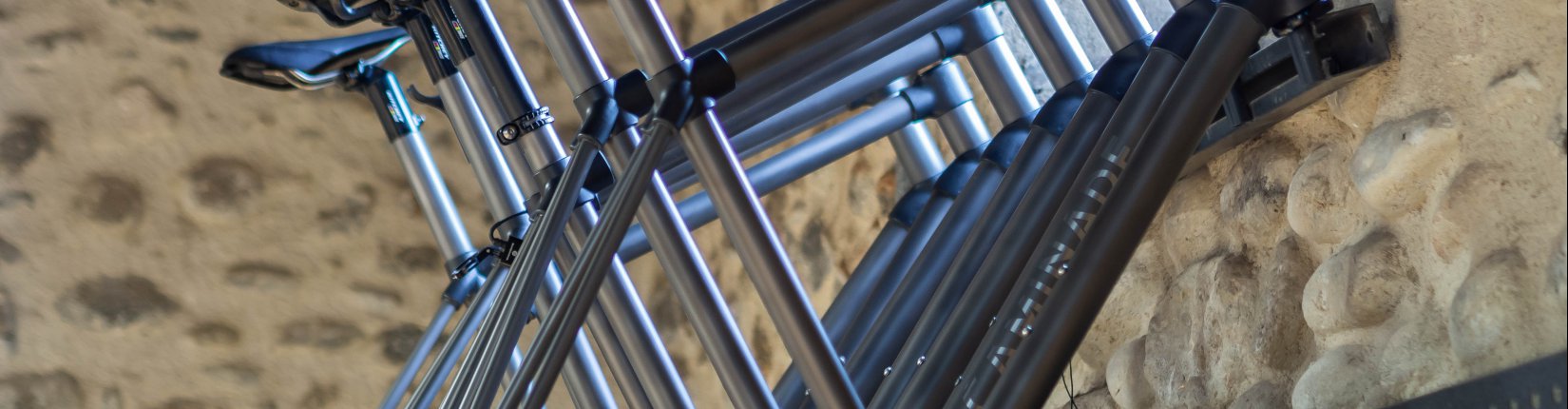
L'Innovation au Service du vélo : La Technologie de Collage Structural chez Caminade
Une Collaboration Visionnaire
En 2017, nous avons été contactés par l'usine AVIATUBE, une entreprise dynamique dont l'objectif était de transposer les technologies de l’aéronautique au service d'autres secteurs industriels. Leur volonté de marier qualité, robustesse et légèreté a rapidement attiré notre attention. Grâce à leurs tubes légers en aluminium qui possèdent une souplesse comparable à celle de l'acier — tout en nécessitant une méthode d’assemblage innovante — nous avons décidé de nous lancer dans l'élaboration de notre premier concept-bike basé sur un assemblage de tubes collés.
Une Approche Technique
Pour mener à bien ce projet ambitieux, nous avons décidé de collaborer avec Axson, un spécialiste reconnu dans le domaine des adhésifs. Nous avons établi un cahier des charges clair, comprenant des critères essentiels : des propriétés mécaniques élevées, une haute résistance au vieillissement et un temps ouvert long pour garantir un assemblage minutieux et précis.
C’est l'adhésif époxy structural ADEKIT H9952 qui a été préconisé par Axson. Afin de valider la taille de la surface de décollage nécessaire à la résistance d'un cadre de vélo, Axson a réalisé trois séries de tests en laboratoire. Pour chaque série de test, nous avons mesuré la force nécessaire à l'arrachage de l'éprouvette, ainsi que la surface réelle de colle, permettant ainsi de déduire une valeur moyenne de résistance en MPa.
initial |
après fluage |
après vieillissement |
après 3 jours à 23°C | 30 minutes à 180°C | 15h à 40°C 2h à -20°C 4h à 70°C |
23,2 Mpa +/- 1,8 |
18,1 Mpa +/- 2,1 | 25,4 Mpa +/- 1,4 |
soit 235,6 kg par cm² de colle |
soit 184,6 kg par cm² de colle | soit 259 kg par cm² de colle |
L'Importance de la Préparation
Lors de nos essais, nous avons découvert que si la préparation des surfaces était primordiale, elle était également facilement reproductible et maîtrisable. Deux étapes étaient cruciales pour garantir une adhérence optimale :
1. Préparation mécanique par sablage : Cette étape a permis d'obtenir une rugosité d'accroche importante.
2. Soufflage et dégraissage : Ces processus éliminent toute impureté, assurant une surface prête à coller.
Cependant, un véritable défi est apparu lors de la maîtrise de la quantité de colle appliquée, tant en surface qu'en épaisseur.
Une Solution Innovante
Pour surmonter cette difficulté, nous avons développé notre propre solution de manchons injectés. Ces manchons possèdent une gorge de double manchonnage qui sert de réceptacle à la colle tout en augmentant la surface de contact. Lors de l'insertion du tube, la colle est chassée vers l'extérieur, débordant de chaque côté, assurant ainsi un joint résistant et homogène.
Résistance et Performance
Sur nos modèles AllRoad, nous utilisons des tubes de quatre diamètres différents. Il est à noter que plus le diamètre est grand, plus la surface de collage est importante, augmentant ainsi la résistance à l'arrachement :
- 5 tonnes pour une jonction de hauban en 16 mm
- 7 tonnes pour une jonction de base en 22,22 mm
- 11 tonnes pour les jonctions du tube horizontal ou du tube de selle en 34,9 mm
- 14 tonnes pour les jonctions du tube diagonal ou de la douille en 44,45 mm
Avant la commercialisation, nous avons également effectué des tests de résistance terrain, tout en préparant le cadre pour son homologation selon la norme ISO 4210-6. Cela a impliqué :
- Trois essais de fatigue, chacun de 100 000 cycles, simulant les forces de pédalage et des charges horizontales et verticales.
- Deux essais de choc, incluant la chute d’une masse et la chute du cadre lui-même.
Un Cadre Homologué
Bien que nous avions la possibilité de tester plusieurs cadres, des contraintes budgétaires nous ont contraints à en envoyer un seul au CRITT de Châtellerault. Ce cadre a passé avec succès tous les tests et a obtenu le numéro d'homologation ES12/17/1899, validant ainsi notre approche de collage structural.
Avantages Économiques
Ce système de collage structurel nous permet également de réduire considérablement les délais et le coût de fabrication des cadres sur mesure, ce qui se traduit par un prix de vente plus compétitif. Grâce à l'innovation dans l'assemblage, qui utilise des manchons en composites pour relier les tubes, nous avons réussi à réduire le temps de fabrication d'un cadre. En effet, le processus est passé de 25 heures pour un cadre mécano-soudé à seulement 4 heures pour un cadre collé. Ce gain de temps significatif nous permet d'optimiser notre production sans compromettre la qualité. Les manchons en composites assurent une liaison solide et durable tout en simplifiant l'assemblage, ce qui permet d'accélérer le processus de fabrication.
Cela se traduit directement par un prix final plus abordable pour nos clients, rendant nos vélos sur mesure accessibles à un plus large public, tout en maintenant une qualité de conception exceptionnelle que nos clients ont appris à attendre de Caminade. Actuellement, deux de nos modèles bénéficient de cette technologie innovante :
AllRoad : modèle gravel à tubes titane, conçu pour l'aventure et la polyvalence.
LongRoad : le vélo de route d'endurance à tubes titane, parfait pour les longues distances et les randonnées sur route.
Une Technique Adoptée par des Leaders
Nous ne sommes pas seuls à adopter cette technique de collage structuré, qui est finalement bien moins artisanale que la réalisation de cadres monocoques, où le drapage manuel est difficilement reproductible :
- Colnago, sur les 2 seuls modèles route fabriqués en Italie
- Atherton, pour ces cadres de DH sur mesure
- Hope, qui a remplacé la soudure sur des haubans aluminium de leur vélo d'enduro par le collage
Parution : 15/11/2018